Die Verlegetechnik von Melaminharz-Böden (Laminatböden)
Kaum fünf Jahre ist es her, daß Melaminharz-Böden, oder einigen wir uns für die nachfolgenden Ausführungen auf das Wort Laminatböden, in beachtenswerter Grössenordnung den Markt erobert haben. Mittlerweile sind die Marktanteile beachtlich, und Laminatböden haben ihre feste Position in der Gruppe der Bodenbelagsarten gefunden. Für uns als Sachverständigenbüro, spezialisiert auf Fussbodentechnik, war dieses Bodenbelagsmaterial ebenfalls neu.
Allein dieser Umstand war natürlich für uns die Herausforderung schlechthin, diese noch geheimnisvolle Bodenbelagsart aus produkt- und verlegetechnischer Sicht zu studieren. In gewohnter Weise haben wir uns an die Arbeit begeben und unzählige Produktdatenblätter mit technischen Erläuterungen und Aussagen studiert. In Kenntnis der Rezeptur und Zusammensetzung von textilen und elastischen Bodenbelägen suchten wir, zugegeben wahrscheinlich aus Gewohnheit, vergleichsweise wie bei Fertigparkett, nach dem kontinuierlichen Feuchtigkeitsgehalt der organischen Trägerplatte oder, wie bei Kunststoff-Bodenbelägen, nach der Dimensionsstabilität.
Mit jeder neuen Erkenntnis kamen zwei neue Fragen hinzu, so daß die Fülle der nunmehr vorliegenden Informationen, durchgeführten Prüfungen und Prüfungsergebnisse einen ersten Abschluß dieser Grundsatzarbeit beschert hat, wobei insgesamt gesehen ein Ende unserer Forschung noch gar nicht abzusehen ist, zumal ständig Produktinnovationen erscheinen. Die nachfolgenden Ausführungen sind nicht der Weisheit letzter Schluß, zeigen aber auf, daß sich die unterschiedlichen Produkte der Laminatböden sicher nicht im Endstadium der Entwicklung befinden.
Es ist um bestimmte Anforderungskriterien, die in der Einführungsphase der Laminatböden akribisch lanciert worden sind, still geworden. Zum Beispiel scheint die Oberfläche dieser eben auch mit Füßen getretenen Bodenbelagsart nicht ganz so kratzfest zu sein, wie man es sich wünschte. Auch das Abriebverhalten wurde als eine Komponente der Qualitätsbestätigung werbemässig genutzt, in dem Glauben, daß schwindelerregende Umdrehungszahlen beim Einsatz eines 100er Schleifpapiers und eines Taber-Abraser-Prüfgerätes gleichzeitig im Praxisgebrauch ein hochwertiges Produkt bestätigen.
Auf diese Weise ist wie von selbst der Zugzwang entstanden, die Oberfläche des besten Produktes mit Abriebwerten bzw. Umdrehungszahlen darzustellen, die fünfstellige Summen überschreiten. Nach unserer Meinung unnötig, denn keiner wird bestreiten können, daß die Oberfläche eines Laminatbodens im Vergleich zu anderen Bodenbelagsarten immer noch ihresgleichen sucht. Zu einem Sachverständigenbüro gehört es, sich mit Reklamationen und Schadenfällen zu befassen, wobei Verschleisserscheinungen oder hieraus resultierende Schäden nicht an der Tagesordnung sind und zudem sehr unterschiedliche, objektbezogene Situationen bei der Ursachenforschung zu berücksichtigen sind.
Schäden sind immer eine Ausnahme, aber in Einzelfällen zeigt sich, daß viel mehr Reklamationen durch nachträglich entstandene Fugen sowie Schüsselungen der Paneele in Längs- und Querrichtung entstehen, wobei auch von Fall zu Fall Beanstandungen aufgrund von Überzähnen im Stossbereich aneinander grenzender Paneele bekannt sind. Zur Ursachenforschung eines Schadens gehört nicht nur eine Produktanalyse, sondern auch die Überlegung und Recherche, warum häufig Verlegefehler, aber auch Unzulänglichkeiten im Gebrauch, d. h. während der Nutzung, Schäden bei Laminatböden verursachen. Bei der Analyse stößt man zwangsläufig auf Widersprüche.
Verlegerichtlinien im Widerspruch
In den Verlegeanleitungen zu Laminat-Paneelen wird überwiegend die VOB, Teil C, DIN 18 365 ‚Bodenbelagsarbeiten‘ als Verlegevoraussetzung genannt. In dieser DIN-Schrift sind ausreichende Hinweise zu Untergründen und Untergrundvorbehandlung zu finden, auch zu der Verlegung/Klebung von textilien und elastischen Bodenbelägen. Mehr oder weniger starre Bodenbelagselemente, wie es Laminat- Paneele sind, oder Hinweise zu der schwimmenden Verlegung von Bodenbelägen befinden sich ebenso wenig in dieser DIN-Schrift wie Erläuterungen zur Verleimung von Nut und Feder usw. Vielleicht war es ein handwerkspolitischer Hintergrund, der in der Einführungsphase von Laminatböden dazu geführt hat, daß nicht die DIN 18 356 ‚Parkettarbeiten‘, die eher einen kausalen Zusammenhang herstellen läßt, als maßgeblich interpretiert wurde. Spätestens seit der Novellierung der Handwerksordnung und der nunmehr nicht mehr wegzudiskutierenden Etablierung der Produktlinie- Laminat-Paneele – in allen fussbodenlegenden Branchen, dürfte das Argument auch nicht mehr diskussionswürdig sein. Im Interesse der Produkthersteller sowie Händler und Verarbeiter bedarf es dringend einer einheitlichen Regelung allgemeiner Anforderungen an den Untergrund sowie Verlegerichtlinien, die dann durch die spezielle Verlegeanleitung zu dem jeweiligen Produkt ergänzt werden. Im Augenblick sollte das oberste Gebot sein, die jeweilige Verlegeanleitung zum entsprechenden Produkt streng, ja sklavisch zu beachten, da ansonsten n Falle einer Reklamation/eines Schadens Diskussionen nicht selten wie das ‚Hornberger Schiessen‘ enden.
Widersprüche in den Produkteigenschaften
Verbraucher- und Anwenderprospekte schreiben zum Beispiel, daß die Trägerplatte des jeweiligen Laminat-Paneels, unabhängig, ob Faserplatte (MDF/HDF) oder Holzfeinspanplatte, feuchtigkeitsunempfindlich oder feuchtigkeitsresistent ist. Wir dürfen hoffen, daß der Anwender, d. h. Verleger der Laminat-Paneele, diese Aussage nicht als Suggestion entgegennimmt und glaubt, das jeweilige Laminat-Paneel sei gegenüber Feuchtigkeit immun. Der Verbraucher, bzw. der Laie, wird dieser Aussage eher Glauben schenken und auch mit dem Hinweis, daß unbedingt nur nebelfeucht (ein ausgewrungenes, tropffreies Wischtuch wird gemeint sein) zu wischen ist, vielleicht schon mal zuviel Feuchtigkeit bei der Reinigung einsetzen und dann wird sich zeigen, ob die Trägerplatte resistent oder beständig gegenüber äußerer Feuchtigkeitseinwirkung ist. Sicher werden sich organische Trägerplatten, d. h. Holzfaser- und Holzfeinspanplatten, bei äußerer Feuchtigkeitseinwirkung nicht in Wohlgefallen auflösen, aber immer eine Reaktion zeigen.
Organische Trägerplatten und Feuchtigkeit
Die Produktelinien der Laminatböden haben, wie bekannt, zumindest den bedeutsamen Ursprung in skandinavischen Ländern. In diesen Ländern pflegt man bei Gebäuden die Trockenbauweise (überwiegend Holzkonstruktionen), während in Deutschland und in der Schweiz die Nassbauweise (Stein/Zement/Beton) immer noch Gepflogenheit ist. Somit haben wir bei immer schneller werdender Bauweise, bei Durchführung von Untergrundvorbereitungs- und Bodenbelagsverlege-Massnahmen zwangsläufig mit zunehmend ungünstigeren, hohen Baufeuchten, d. h. letztlich mit hohen relativen Luftfeuchten, zu kämpfen.
Zusätzliche Feuchtigkeit erfahren die Laminat-Paneele bei der schwimmenden Verlegung durch die Nut- und Federverleimung, bei der der Leim einen Wassergehalt von mindestens 40 Prozent ausweisen dürfte. Soll bei der Nutzung bzw. beim Begehen der Laminatböden der akustisch wahrnehmbare Effekt ‚Barackeneffekt‘ vermieden werden, ist die vollflächige Klebung der Laminat-Paneele zusätzlich zu der Nut- und Federverleimung gewünscht. Während Polyurethanklebstoffe ein weitgehend zufriedenstellendes Verlegeergebnis kalkulieren lassen, werden auch gern Dispersionsklebstoffe eingesetzt, die wiederum einen Wassergehalt von mindestens 20 Prozent eventuell auch 30 Prozent aufweisen, weniger gewiß. Praxisbezogen entsteht somit häufig folgende Situation:
Im Dienstleistungszeitalter ist Schnelligkeit gefragt und das Argument, morgens verlegt – abends bewohnt, öfter zu hören. Eigentlich ist in so einem Fall die Reklamation vorprogrammiert. So hart und kraß das nachfolgende Beispiel ist, so oft kommt es in der Praxis vor.
- Morgens Wohnzimmer ausgeräumt,
- alten textilen Bodenbelag entfernt, Untergrund geschliffen und abgesaugt,
- Laminat-Paneele mittels Dispersionsklebstoff vollflächig geklebt sowie nut- und federverleimt,
- Sockelleisten montiert,
- Laminatboden schnell übergewischt,
- Wohnzimmer eingeräumt.
Dass es so nicht geht (aber dennoch gemacht wird), ist jedem bekannt. Eine mögliche Reklamation infolge Schüsselungen der Laminat-Paneele und/oder Fugenbildungen (siehe Fotos 1 und 6) wird in der Ursache (siehe Fotos 3 und 4) nachvollziehbar analysiert.
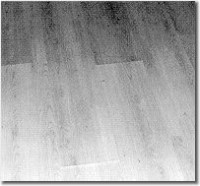
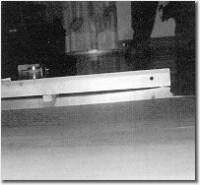
Foto 1 und 2 zeigen aus unterschiedlichen Perspektiven erhebliche Aufschüsselungen von Laminat-Paneelen sowohl in der Längsrichtung als auch in der Breite.
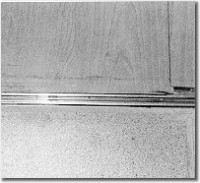
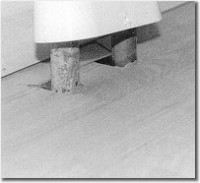
Die wohl häufigste Ursache der Aufwölbungen von Laminat-Paneelen und Laminatflächen sind wie auf Foto 3 und 4 ersichtlich fehlende Raum-/Randfugen, die eine Ausdehnung der Laminat- Paneelflächen verunmöglichen.
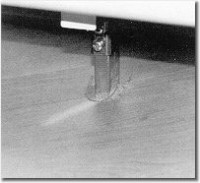
Ein Bodenleger hatte die Bewegungsfuge im Bereich von Heizungsrohren und Standfüssen einfach zuzementiert.
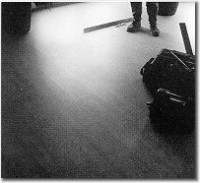
Bei entsprechender systematischer Vorgehensweise sind bei der Schadenursachenforschung am einfachsten handwerkliche Unzulänglichkeiten (zum Beispiel unzureichende Verleimung von Nut und Feder oder Anarbeiten der Laminat-Paneele an feststehende Bauwerksteile usw.) nachvollziehbar, da optisch erkennbar. Wir haben uns für die Grenzfälle interessiert, wo nicht eindeutig erkennbar war, warum nun die jeweilige Laminatbodenebene in der Verlegeeinheit, d. h. im Oberflächenbild, nicht so beschaffen ist, wie es die Fotos der Prospekte versprechen, bzw. es in der Folge der Verbraucher erwartet. Aufgrund der Tatsache, daß in der Fussbodentechnik die Holzspanplatte am weitesten verbreitet ist, durfte hier die Analyse zur Ermittlung der Einflussfaktoren der Dimensionsveränderung von organischen Trägerplatten als Schwerpunkt angesetzt werden.
Die Art und Weise der Nachbehandlung von Verlegeplatten bzw. Holzspanplatten V 100 E1, in der Mindestdicke von 19 Millimetern, ist bekannt. Im Trockenausbau finden diese Platten oft Einsatz, wobei auch zementgebundene Spanplatten bekannt sind. jeder, der schon einmal Holzspanplatten (oder auch zementgebundene Spanplatten) verlegt hat, weiß, daß Nut und Feder verleimt werden und zumeist die Notwendigkeit besteht, bei der Untergrundvorbehandlung die Stössezuschleifen und abzuspachteln, da diese nicht selten kleine Aufschüsselungen, d. h. Unregelmässigkeitenzeigen. Für uns stellt sich die Frage, ob es möglich wäre, plötzlich die physikalischen Eigenschaften von Holzspanplatten oder allgemein von organischen Trägerplatten so massiv zu optimieren (zum Beispiel durch oberflächige Laminierung und Gegenzuglaminat), daß gänzlich die physikalischen Eigenschaften bis ins Unerkennbare dezimiert würden.
Analyse zur Ermittlung der Einflussfaktoren
Die folgenden Erläuterungen zur Ermittlung der relevanten Einflussfaktoren bei Dimensionsveränderungen von organischen Trägerplatten bzw. Holzfeinspanplatten verschafft aus unserer Sicht einen Überblick, angefangen vom Rohstoff über die Trägerplatte bis hin zum Endprodukt des Laminat- Paneels:
- Für die Herstellung entsprechender Platten werden folgende Hölzer eingesetzt:
– Hartlaubholz: Edelkastanie, Ahorn, Rüster, Birke, Akazie und Hainbuche
– Weichlaubholz: Pappel, Linde, Erle, Weide
– Nadelholz: Fichte, Kiefer
– Sonstige: Rinde, Sägespäne, Schleifstaub, Grüngut. - Verschiedene Hölzer bedingen natürlich auch andersartige Beschaffenheiten wie:
– unterschiedliche Holzfeuchte
– unterschiedliches Quellen und Schwinden
– unterschiedlicher Feuchtigkeitsfasersättigungsgrad
– schwankender pH-Wert - Zur Rohstoffaufbereitung werden die Hölzer gesammelt, gehackt, zerspant, gemahlen, sortiert, gebunkert, getrocknet und gesichtet. Aufgrund dieser unterschiedlichen Prozesse können Reaktionen auftreten (im ungünstigsten Fall Fäulnis). Die Spanform kann sich mit der Bearbeitung des Holzes verändern. Diese aber hat wesentlichen Einfluß auf die Biegefestigkeit, die Dickenquellung und auf die Beschaffenheit der Schmalfläche.
- Als Harze der Spanplatte werden überwiegend Phenol-Formaldehydharze (KPF), Normtyp V 100 oder Melamin-Formaldehydharze (KMF), Normtyp V 100 verwendet. Bei langandauernder Feuchtigkeitseinwirkung ist die Gefahr eines hydrolytischen Abbaus gegeben.
- Weitere Zusatzstoffe sind Isocyanate, Tannin-Formaldehydharz und Hydrophobierungsmittel. Bei mehr als 1 Prozent Festparaffin (feuchtigkeitsabweisendem Schutzfilm) auf die atro-(absolut trockene)-Holzmasse kommt es zur Beeinträchtigung der Verleimung.
- Als nächster Schritt zur Herstellung von Spanplatten erfolgt die Verpressung. Dabei ist zu beachten:
– Vorpressung geschieht kalt, jedoch meist mit Hochfrequenz-Vorwärmung
– hohe Decklagenverdichtung
– schnelles Pressen mit hohem Druck
– hohe Querzugfestigkeit
– langsamer DruckaufbauPresszeiten sind abhängig von der Presstemperatur und den Bindemitteln. Ungleichmässiger Druck bei verschiedenen Temperaturen führt zu Vorhärtungen, Verdichtungen und Abnahme der Leimbindefestigkeit. Zudem kann eine ungleichmäßige Verteilung der Deckschichten und Mittelschichtspäne erfolgen. - Das Konditionieren erfolgt durch Rückkühlung der verpressten Platten vor der Einlagerung, das heißt Endfertigung oder Weiterverarbeitung in sogenannten Stern- oder Kühlwendern. Je dünner die Platten sind und je höher deren Rohdichte ist, um so größer ist der Feuchtigkeitsstau in der Mittellage. Bei der Abkühlung tritt in der Mittellage ein gewisser Schwund ein (etwa’/,o Millimeter). Übertrocknete Decklagen nehmen nach dem Verlassen der Presse reichlich Feuchtigkeit aus der Umgebungsluft und der feuchteren Mittellageauf. Neben dem Schwund in der Plattenmitte kann es zum Anquellen der Plattenränder kommen. Diese Erscheinungen treten verstärkt in den Wintermonaten bei größeren Temperatur- und Feuchtigkeitsunterschieden auf. Als Folgeerscheinung des Feuchtigkeitsausgleichs kommt es zu einer Längenausdehnung (Quellung in Plattenebene) der Decklagen, verbunden mit einem Schrumpf der Mittellage. Hierdurch entstehen Spannungsdifferenzen innerhalb der Platte zwischen Deck- und Mittellage. Nur wenn diese Spannungen leicht sind, bleibt die Platte formstabil.
- Zur Endfertigung wird die Rohspanplatte besäumt, geschliffen, sortiert, gelagert, zugeschnitten, in Fixmasse aufgeteilt und transportiert. Unterschiedliche Feuchte in verschiedenen Bereichen der Platten kann auftreten, bedingt durch die Lagerung sowie den Transport zum Beschichten.
- Die Beschichtung bzw. Laminierung der Rohspanplatte sollte optimalerweise nach folgenden Kriterien erfolgen:
– feine Decklagenspäne (über 60 Prozent < 0,6 Millimeter)
– drucksteife Mittellage (möglichst Buche)
– Festharzgehalt in der Mittellage, mindestens 7 Prozent auf atro-Holzmasse
– Querzugfestigkeit, mindestens 0,5 N/mmZ
– Rohdichte, mindestens 650 kp/m3 Plattenfeuchte nicht über 8 Prozent
– Decklagenrohdichte, mindestens 12 Prozent auf atro-Holzmasse
– bei Folienbeschichtungen treten Zugspannungen bis zu 50 N/mmZ auf.
Die Fülle der wesentlichen Qualitätsmerkmale scheint mit vertretbarem Aufwand nicht fortlaufend bestimmt zu werden, so daß der Prüfungsumfang je nach Hersteller, in der uns bekannten Form, zwischen 0,1 bis 0,5 Prozent der Spanplattenfertigung schwankt. Somit erscheint das Hauptkriterium und daraus resultierende Problem beim Beschichten in den Qualitätsschwankungen bzw. Schwankungen der kennzeichnenden Merkmale der zugelieferten Rohspanplatten zu liegen. Ferner ist zu berücksichtigen, daß mit steigender Härte der Oberfläche immer größere Anforderungen an das Trägermaterial gestellt werden.
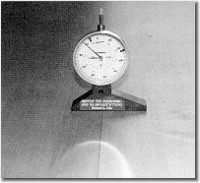
Sind Überzähne bis maximal 0,2 Millimeter im Bereich aneinandergrenzender Stosskanten der Laminat-Paneele (hier: 0,1 mm) grundsätzlich ein Reklamationsgrund?
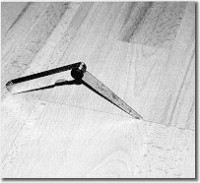
Dürfen Laminat-Paneele in keinem Fall Schwindfugen bis zu 0,5 Millimeter zeigen?
- Die Einflussfaktoren für die Klebfestigkeit der Holzleime (B3/D3), in Verbindung mit den Holzfeinspanplatten als Träger für Laminat- Paneele, sind zahlreich:
– Art und Zusammensetzung des Klebstoffes
– Klebstoffeinsatzmenge
– Verklebungsart
– Holzart (Art der Fügeflächen)
– Größe, Form und Oberflächenbeschaffenheit
– Feuchte und Temperatur der Fügestoffe
– Raumklima (Temperatur und relative Luftfeuchtigkeit)
– Pressbedingung (Temperatur, Druck, Zeit) - Die aufgeführten Einflussfaktoren sind wie folgt zu spezifizieren:
- Art und Zusammensetzung des Klebstoffes: Verwendet werden Polyvinylacetatleime-Weissleime, welche als Holzleime in gebrauchsfertiger Dispersion oder Emulsion mit Feststoffgehalt zwischen 50 und 60 Prozent im Handel erhältlich sind. Durch Zugabe von Isocyanaten konnte die Beständigkeit bei starker, mechanischer sowie klimatischer Belastung erheblich verbessert werden. Gemäß DIN 68 602 ist Laminatleim als B-3-Leim eingestuft (heute D-3-Leim nach EN 204). Durch Einwirkung von beispielsweise Licht, Wärme, Feuchte, Sauerstoff sowie Weichmacherwanderung und Weiterführung der Polymerisation kann eine Veränderung der Molekularstruktur des Klebstoffes eintreten, die eine Versprödung oder Erweichung der Klebefuge zur Folge hat.
- Die Klebstoffeinsatzmenge richtet sich nach verschiedenen Faktoren:
– Beschaffenheit des Klebstoffes (Feststoffgehalt)
– Beschaffenheit der Fügestoffe (Passgenauigkeit von Nut und FederDas Abdiffundieren des Wasseranteils aus der Klebfuge während des Abbindens ist dabei mit starken Schrumpfungsbewegungen des Klebstoffes verbunden. Da das Abbinden der Abwanderung des Dispersionsmittels nach unserem Kenntnisstand offenbar vorauseilt, entstehen erhebliche Schrumpfungsspannungen, die um so größer sind, je dicker die Klebfuge ist.
In diesem Zusammenhang ist zu berücksichtigen, daß überwiegend bei der Leimung von Laminat-Paneelen seitens der Hersteller vorgegeben wird, die Nut vollsatt mit Leim zu füllen, so daß diese dann auf die Feder der jeweils angrenzenden Paneele gepreßt wird, bis der Leim nach oben ausquillt und abgestrichen werden kann. Bei spröden Klebstoffen führen Spannungen in kurzer Zeit zu Spannungsrissen in der Klebstoffschicht. Gute Leime zeigen sich hierbei sehr elastisch, so daß in diesem Zusammenhang nach unserem Kenntnisstand eine größtmögliche Sicherheit gegeben ist, wenn nicht zuviel Leim eingesetzt wird. Hierbei gilt gemäß unseren Versuchen: „so dünn wie möglich, so dick wie nötig“, wobei eine dünne Klebfuge= < 0,1 Millimeter und eine dicke Klebfuge= > 0,1 Millimeter ist.
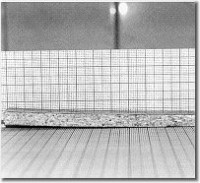
Diese Aufnahme zeigt eine organische Trägerplatte/Laminat-Paneele bei Feuchtigkeitseinwirkung
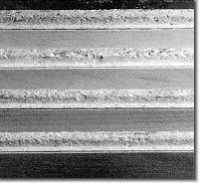
- Bei der Verklebungsart präsentiert sich die anwendungstechnische Empfehlung, die schon oben erwähnt worden ist, folgendermaßen:
Einflussfaktor = die anwendungstechnisch schwierige, korrekte Ausführung der Leimauftragsmenge - Holzart, Größe, Form und Oberflächenbeschaffenheit: Die Güte und Dauerhaftigkeit der Klebung/ Leimung hängt im wesentlichen von der Oberflächenbeschaffenheit der Fügestoffe (Nut und Feder) ab. Je rauher die Oberfläche der Fügeteile (Nut und Feder), desto dicker die Klebfuge. Dadurch kann es zu ungenügender bzw. fehlender Klebfestigkeit und daraus resultierend zu einer mangelhaften Fugenbeständigkeit kommen. Bei glatten Fügeflächen und somit dünnen Klebfugen besteht keine kritische Rissgefahr. Bestimmte Lösungsmitte) oder auch Holzschutzmittel innerhalb der Fügematerialien/-flächen wirken quellend oder anlösend bei verschiedenen Klebstoffen. Auch Weichmacherzuwanderung aus dem Fügematerial in die Klebfuge kann die Kohäsion schwächen, wie auch eine Alterung der Fügestoffe sich auf die Klebeverbindung (Adhäsion) auswirken kann. Ein weiterer Einflussfaktor ist unterschiedliches Dehnungsverhalten der verklebten Fügestoffe, zum Beispiel durch verschiedene Eigenschaften der Trägermaterialien der einzelnen Paneele (V 100 G/Verträglichkeitsnachweis für Klebstoffe).
- Die Haushaltsfeuchte der Fügestoffe sowie das Raumklima haben einen entscheidenden Einfluß auf die Funktionsweise der Klebfuge. Bei Untertrocknung der Fügestoffe kommt es zu Schwindspannungen, bei Feuchtigkeitszunahme zu Quellspannungen und bei Feuchtigkeitsdauereinwirkung zur Plastifizierung der Klebfuge. Die Fugenfestigkeit sinkt bereits mit Zunahme der relativen Luftfeuchtigkeit. Die empfohlene Haushaltsfeuchte sollte 6 bis 10 Prozent sein, die empfohlene relative Luftfeuchtigkeit 60 Prozent, die empfohlene Lufttemperatur 20 Grad Celsius und die empfohlene Bodentemperatur 18 Grad Celsius.
- Pressbedingung: Ein hoher und gleichmäßiger Druck während der Abbindezeit gewährleistet eine einwandfreie Klebfuge. Ebenso sind eine gute Abstimmung zwischen Klebstoff und Fügestoff sowie geeignete klimatische Bedingungen entscheidend.
- Einflussfaktoren sind:
– zu geringer und vor allem zu früh gelöster Druck auf Nut und Feder (zum Beispiel zu frühes Lösen der Abstandsklötze)
– ausgeübter Druck bis zur Abbindezeit bis 0,2 – 0,5 N/mmz unzureichende, d.h. falsche klimatische Bedingungen. - Definition der Haushaltsfeuchtigkeit/Materialfeuchtigkeit der Trägerplatten der Laminat-Paneele: In allgemeinen technischen Unterlagen/Produktinformationen zu Laminat-Paneelen dieser Art sind keine Angaben zur Haushalts-/Materialfeuchtigkeit zu entnehmen. Bis zum heutigen Zeitpunkt scheint seitens der Hersteller und Lieferanten von Laminat-Paneelen nicht bekannt bzw. definiert zu sein, wie groß der Feuchtigkeitsgehalt der Trägerplatten in Gewichtsprozenten ist. Eine einheitliche Regulierung des Feuchtigkeitsgehaltes von Holzfeinspanplatten als Trägerplatten darf insofern angezweifelt werden, da bei gleichen Produktqualitäten Feuchtigkeitsgehalte zwischen 4,8 bis 7,9 Gewichtsprozenten gemessen worden sind und andere Produkte gleicher Art und Beschaffenheit in dem Holzfeinspanplattenträger bis 8,8 Gewichtsprozent Feuchtigkeit aufwiesen.
In gleicher Weise erscheint eine gewisse Unregelmäßigkeit bei Holzfaserplatten (MDF/HDF). Nach unseren derzeitigen Erkenntnissen infolge des Produktionsablaufes von Trägerrohplatten und der Laminat- Paneele sind ungleiche Feuchtigkeitsgehalte innerhalb der Trägerplatte vorprogrammiert. Es ist zudem nicht auszuschließen, daß einerseits untertrocknete Trägerplatten vorliegen und andererseits überfeuchtete, so daß das Spannungsverhältnis innerhalb der Paneele selbst angereichert ist und durch Spannungen der ober- und unterseitigen Laminierung keine ausreichende ‚Sperrung‘ der Platte entsteht. Die Folge sind Verformungen, d. h. Dimensionsveränderungen. In so einem Fall wird dann auch die Verlegung von Laminat-Panee len auf flächenbeheizte Lastverteilungsschichten (schwimmend oder auch geklebt) mit einem gewissen Risiko behaftet sein, da nicht auszuschließen ist, daß zum entsprechenden Zeitpunkt überfeuchtete Trägerplatten durch ständiges Beheizen schwinden und Fugenabrisse entstehen. Umgekehrt ist auch nicht auszuschließen, daß Laminat-Paneele, die zum Zeitpunkt der Verlegung möglicherweise einen sehr geringen Feuchtigkeitsgehalt aufgewiesen haben, Dimensionsveränderungen, d. h. Quellungen erfahren und die Längenänderungen Quell-/Schubspannungen verursachen, so daß Aufwölbungen, die als Schüsselungen erkannt werden, entstehen.
- Was verursachen nicht vermeidbare Längen- und Breitenänderungen einzelner Paneele? Entstehen während der Verlegung der Paneele oder unmittelbar hinterher entweder durch äußere Einflüsse oder Produkteinflüsse Längenänderungen, wird zwangsläufig die Verleimung der Nut-und Federbereiche, d.h. der Fügeflächen beeinträchtigt, denn:
– Die Güte- und Dauerhaftigkeit der Klebung/Leimung der Fügeflächen (Nut und Feder) wird im wesentlichen von der Oberflächenbeschaffenheit der Fügestoffe/ -flächen tangiert.
– Je rauher die Oberfläche der Fügeteile (Nut und Feder), desto dicker ist die Klebefuge.
– Je dicker die Klebefuge, desto geringer ist die Klebfestigkeit und daraus resultierend eine mangelhafte Fugenbeständigkeit bzw. größere kritische Rissgefahr.
– Bewegungen innerhalb der Abbindephase des Fugenleims entstehen durch Dimensionsveränderungen der Laminat-Paneele, so daß bereits in diesem Stadium das kohäsive Verhalten des Fugenleims beeinträchtigt vorliegt.
– Bei eventuell vollflächiger Klebung mittels eines Dispersionsklebstoffes nehmen zwangsläufig die Holzfeinspanplatten/Trägerplatten Feuchtigkeit auf, die eine Dimensionsveränderung der Laminat- Paneele zur Folge hat.
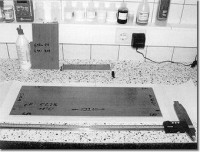
Um zu gesicherten produkttechnischen Erkenntnissen bei Laminat- Paneelen zu gelangen, wurden im Institut für Fussboden- und Raumausstattung eine Reihe von Tests durchgeführt
Schlußfolgerungen
Die technisch nachvollziehbaren Fakten lassen erkennen, daß ein Verarbeiter von Laminat-Paneelen auch bei sklavischer Beachtung der produktspezifischen Verlegerichtlinie/Anleitung die grundsätzlichen Eigenschaften des Produktes selbst oder das der organischen Trägerplatte nicht kalkulieren kann und zu einem bestimmten Grad das Verlegeergebnis einer Laminatbodenfläche und die Gebrauchseigenschaften sowie die zum späteren Zeitpunkt im Wechselfall entstehenden Situationen (Schwindfugen, Aufwölbungen, Verformungen usw.) mit einem beträchtlichen Restrisiko nicht beeinflußt werden können.
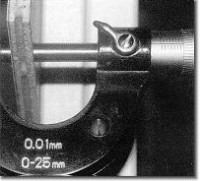
Die im Labor durchgeführten Prüfungen der Dickenquellung von organischen Trägerplatten bei Einwirkung von Weissleimen (B-3- Holzleimen).
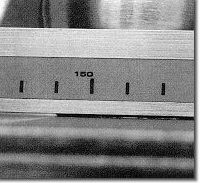
Auswirkung der Quellung einer organischen Trägerplatte im Kantenbereich. Aufschlüsselung der Kante durch Lichtschein unter Strahllineal erkennbar.
Zumal dem Verleger über das Produkt selbst bzw. dem Verhalten der organischen Trägerplatten zuwenig bekannt ist. Eskalieren wird diese Situation eindeutig bei der vollflächigen Klebung mittels eines Dispersionsklebstoffes, da aufgrund der Verschiedenheit der Eigenschaften der Trägerplatten gar nicht abgeschätzt werden kann, wie die Trägerplatten auf den Risikohauptfaktor der Feuchtigkeitszufuhr -den Wasseranteil des Dispersionsklebstoffes- reagieren.
Wird der Unsicherheitsfaktor der differierenden Eigenschaften von Trägerplatten nicht ausgeschaltet, ist nicht mehr auszuschließen, daß gestern die Klebung mittels Dispersionsklebstoff funktionierte, heute oder zwischendurch mal nicht, und in der Zukunft wieder technisch einwandfrei durchführbar ist. Bleiben die Reaktionen der organischen Trägerplatten bei Feuchtigkeitszufuhr so unterschiedlich (sie ist in Abhängigkeit der Art und Beschaffenheit durch die vorherigen Ausführungen nunmehr bekannt), so ist in der Konsequenz, wenn eine vollflächige Klebung unbedingt gewünscht wird, ein geeigneter Polyurethan-Klebstoff risikominimierend.
Keinesfalls ist es uns möglich, in diesem Beitrag alle relevanten und wichtigen Faktoren über organische Trägerplatten und der damit in Verbindung stehenden Eigenschaften aufzuführen.
Wichtig erscheint uns abschließend der Hinweis, daß die Notwendigkeit besteht, daß zwischen den Laminatböden-Herstellern und -Vertreibern auch Einigkeit darüber erzielt werden sollte, daß nicht jede Laminatbodenfläche so ‚topfeben‘ aussehen kann, wie es die Produktbroschüren versprechen.
Organische Trägerplatten bringen entsprechend ihrer Eigenschaften naturgemäß Toleranzen mit sich, so daß von Fall zu Fall nicht zu vermeiden ist, daß:
- Aufschüsselungen im Stossbereich aneinander grenzender Paneele bis 0,2 Millimeter entstehen können, so daß insbesondere bei Gegenlichtbetrachtung sich innerhalb der Verlegeeinheit die einzelnen Paneele abzeichnen (siehe Fotos 1 und 6).
- Überzähne im Stossbereich aneinander grenzender Laminat- Paneele bis maximal 0,2 Millimeter entstehen können (siehe Foto 7).
- Schwindfugen bis maximal 0,5 Millimeter Breite nicht immer vermeidbar sind (siehe Foto 8).
Die Ausarbeitung und Erkenntnisse zum Thema Laminatböden werden sich im Hause des Institutes für Fußboden- und Raumausstattung bei Erscheinen dieses Fachbeitrages weiter entwickelt haben, so daß wir auch in Zukunft über dieses Thema berichten werden.
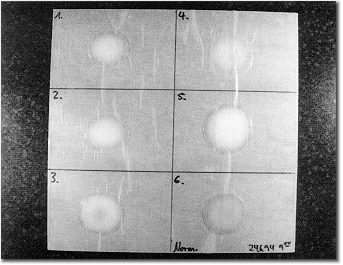
Gezeigt werden sechs im Handel erhältliche, für die Laminat-Paneel-Verleimung empfohlene Weissleime (PVAC-Leime), Güteklasse B 3/D 3. Tests zeigen deutliche Unterschiede der Leime in ihren Eigenschaften.
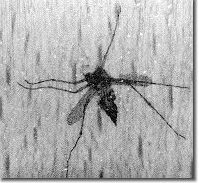
Bei aller Nüchternheit auch eine amüsante Situation: ein reklamiertes Laminat-Paneel, bei dem sich auf der Dekorschicht eine Mücke verewigt hat.
ö.b.v. Sachverständiger Richard A. Kille
c/o IFR-Sachverständigenbürogesellschaft für Fussbodentechnik und Raumaustattung, Köln
Quelle: RZ-Raumaustatter Zeitschrift, München