Redaktionelle Veröffentlichung der BodenWandDecke, Ausgabe 01/2007
(Holzmann Verlag)
Thermisches Verschweißen von PUR-beschichteten Belägen Testergebnisse zeigen Unzulänglichkeiten in der Praxis
Einwandfreie Schweißnaht Zufall
Werkseitige PUR-schutzversiegelte Kunststoff-Bodenbeläge stellen im Vergleich zu unbehandelten Oberflächen heterogener und homogener Kunststoff-Bodenbeläge besondere Anforderungen an die Art und Weise der thermischen Verschweißung.
Der Berufssachverständige Richard A. Kille erläuterte auf dem Sachverständigenseminar in Kassel die Problematik.
„Die Erfahrungen der vergangenen Monate haben gezeigt, dass einerseits die Verarbeiter dieser modernen Kunststoff-Bodenbeläge nicht über jedes Detail Bescheid wissen und andererseits die Hersteller selbst manchmal überrascht sind, welche Situationen nach dem thermischen Verschweißen werkseitig schutzversiegelter Kunststoff-Bodenbeläge entstehen“, skizziert Richard A. Kille, ö.b.u.v. Sachverständiger der HWK Köln für das Raumausstatterhandwerk, Bodenlegergewerbe und Parkettlegerhandwerk, das Dilemma.
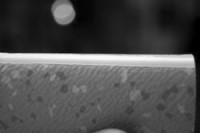
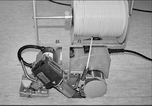
Kille nannte einige Beispiele aus der Praxis, bei denen beschichtete PVC-Beläge, die wie üblich mit einer 4 mm breiten Schweißnaht versehen waren, sich optisch so darstellten, als wäre diese nahezu 3 cm breit. Bei genauerem Hinsehen zeigt sich folgendes Phänomen:
In etwa 1 bis 1,5 cm breiten Streifen parallel zur Schweißnaht werden feine Haarrisse sichtbar, die mit mikroskopischen Aufnahmen einwandfrei zu dokumentieren sind.
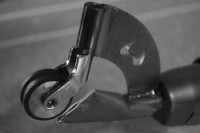

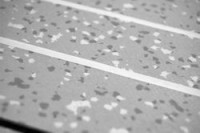

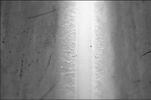
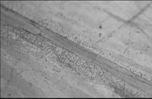
Diese Risse sind dafür ursächlich, dass bei der Reinigung unsaubere, meist bräunliche Schmutzreste sichtbar werden. Kille kennt ähnliche Probleme bei Polyolefinbelägen.
Als auf diese Beläge jüngst zusätzliche Folien-Schutzschichten werkseitig aufgebracht wurden, kam es regelrecht zu Runzelbildungen der Schutzfolien links und rechts zur thermischen Verschweißung.
Erst die Einführung spezieller Schnellschweißdüsen schaffte Abhilfe. Genau an dieser Stelle sieht Kille auch bei elastischen PVC-Bodenbelägen den Ansatz.
„Die speziellen Schnellschweißdüsen haben einen besonderen, schmalen Luftaustritt. Dieser gewährleistet, dass die Strömung der heißen Luft sich soweit wie möglich auf den gefrästen Fugenraum sowie auf die Unterseite des Schweißdrahtes begrenzt. Der Luftaustritt sollte keinesfalls breiter sein als 0,9 mm.
Je breiter der Luftaustritt einer Schweißdüse ist, desto mehr trifft die mit über 180 °C ausströmende Luft auch auf die Oberfläche des Bodenbelages links und rechts der gefrästen, thermisch zu verschweißenden Fuge“, sagt Kille.
In der Vergangenheit wurde der Verarbeiter und Anwender entsprechender Werkzeuge/Geräte beim Verschweißen von PVC-Bodenbelägen aufmerksam, wenn sich beidseitig zu der Naht eine glänzende Spur zeigte.
Erfolgte in klassischer Weise eine Grundreinigungsmaßnahme und anschließende Einpflege, die eigentlich nichts anderes als eine Beschichtung war, wurden diese aus „Fehlleistungen“ resultierenden Begleitspuren neutralisiert.
Doch bei PUR-beschichteten Belägen ist dem nicht so, denn deren thermische Verschweißung scheint noch nicht bis ins Letzte ausgeklügelt, zumal die theoretische Machbarkeit wenig nutzt, wenn das entsprechende Gerät nicht zur Verfügung steht.
Während das oben geforderte Equipment für ein Handschweißgerät vorhanden ist, scheint die notwendige Fußbodendüse mit schmalem Luftaustritt für einen Schweißautomaten eher unbekannt zu sein.
Erst nach umfangreichen Recherchen bei einem bekannten Maschinenhersteller fand Kille die gesuchten schmalen Düsen. Entsprechend zufriedenstellend waren die Prüfungsergebnisse in dessen Versuchsreihen. Diese wurden bei unterschiedlichen Luftaustrittstemperaturen bzw. Laufgeschwindigkeiten der Geräte durchgeführt, um die richtige Einstellung für die optimale Haftung und Verschmelzung der Materialien bzw. die optischen Anforderungen an die Schweißnaht zu finden.
Genereller Tipp für die Praxis: Möglichst vor Beginn der Arbeiten in unzugänglichen Bereichen oder auf Reststücken baustellenspezifische Probeeinstellung der Schweißautomaten vornehmen.
Die gängigen Schweißautomaten mit breiteren Austrittsdüsen zeigten in den Testreihen demgegenüber sehr unbefriedigende Ergebnisse.
Kille kam zu der durchaus bemerkenswerten Erkenntnis, dass PUR-beschichtete PVC-Beläge sich mit herkömmlichen, marktgängigen Geräten zum gegenwärtigen Zeitpunkt nicht fachgerecht verschweißen lassen.
„Zu filigran“, sagt der Experte, „ist zudem das Jonglieren mit der Temperatureinstellung des Schweißautomaten (400 °C bis 600 °C) sowie der Vorlaufgeschwindigkeit (m/min) als auch der Einstellung des Luftvolumenstromes.
„Nahezu eine, Uhrmacherleistung‘, die bei manch einem Belag selbst bei solchem Können nicht zu einwandfreien Ergebnissen führt“, beschreibt der Fachmann die handwerkliche Herausforderung. „Unabhängig davon, dass der Verarbeiter bzw. Auftragnehmer bereits damit zu kämpfen hat, dass thermisch verschweißte Nähte bei PVC-Bodenbelägen keine Schutzversiegelung aufweisen und gelegentlich Nahtanschmutzungen reklamiert werden, können sich links und rechts der thermischen Verschweißungen – je nach Farbgebung des Belages – auf einer Gesamtbreite von bis zu 2–3 cm dunkle Streifen, letztlich Schmutzpartikelanhäufungen zeigen, die dann Grund von Reklamationen sind“, moniert Kille die ungewohnte „Hypersensibilität“ dieser Systeme. Folglich besteht auch beim anschließenden Abstoßen der Schweißnaht im Zuge der erforderlichen Arbeitsschritte mit geeignetem Gerät (Viertelmond) die Gefahr, dass die Beschichtung verletzt wird.
Kille fand bei seinen Versuchsreihen zwar eine handwerkliche Lösung des Problems, indem er „mit äußerster Vorsicht und bei gerader Haltung“ mit einem Handföhn arbeitete und einen entsprechend schonenden Abstoßspachtel, mit dem beispielsweise beim Abstoßen des Schmelzdrahtes bei der Verfugung von Korklinoleum gearbeitet wird, einsetzte, aber praxisüblich befand er dieses Vorgehen keineswegs.
Nach konkreten Erfahrungen im dritten Großprojekt mit PUR-schutzversiegelten Kunststoff-Bodenbelägen unterschiedlicher Hersteller sieht Kille eindeutig Handlungsbedarf.
Er regt daher an, mit den Werkzeug und Geräteherstellern zu überlegen, ob die alten, klassischen Geräte letztlich gegebenenfalls modifiziert werden können, damit wieder ein „Sicherheitspuffer“ entsteht, der das Gelingen einer optisch und technisch einwandfreien Schweißnaht nicht dem Zufall überlässt.
Quellennachweis: BodenWandDecke, Ausgabe 1, Januar 2007